How to Increase Speed and Precision in Recall Management
What is preventing the fast, precise identification of contaminated products in the event of a food safety event? The lack of data. Data that can immediately, and specifically pinpoint the exact product causing the illness. Data that allows for end-to-end supply chain collaboration so the correct contaminated product is removed. This is what can save lives, save your brand, and save goods from being unnecessarily wasted during a contamination event.
Access to this essential data has not existed for the industry, until now.
iTradeNetwork has cracked the code to instant, precise incident and recall management with the industry’s first and only traceability system that relies on data and machine learning, not just labels. This solution allows you to identify and remove contaminated goods within seconds of an alert from the CDC and FDA, instead of days.
Before we go into how this new technology will transform traceability for the industry and your business, let’s look at why such a modernized traceability solution is important to have as food safety events become more and more common.
Current Food Safety & Recall Response
The push to ensure food safety through traceability has been a major priority for the government and food industry as food recalls have increased in the past decade.
From the industry-led Produce Traceability Initiative (PTI) to the Food and Drug Administration’s proposed stricter rule that would go above and beyond the requirements set in the original 2011 FDA Food Safety Modernization Act (FSMA), increased end-to-end traceability through new rules and regulations will continue in order to protect consumers.
The new requirements of FSMA section 204, Enhancing Tracking and Tracing of Food and Recordkeeping, will mandate:
- How traceability records must be maintained
- You must provide records within 24 hours of a request
- Your data and records are organized electronically, not manually.
This means suppliers and buyers need to be able to modernize their systems not only to adhere to these changing regulations but also to be able to coordinate during a recall event.
Traditional Traceability Challenges
Right now, buyers and suppliers have traceability systems in place, but even with PTI, the traditional solutions still leave businesses to the risks of recalls. Why? Because they are working with incomplete, fragmented data and individual approaches to risk. This lack of collaboration, consistency, and real-time, accurate data is keeping companies from moving forward with faster food safety event responses.
Three of the biggest current problems that impact the time and accuracy of food safety events include:
- Incomplete product origination data
Yes, PTI is a universal standard, but it’s not universally adopted across the supply chain due to cost and process burdens.
- Lack of common, trusted, data
If suppliers and/or retailers are still managing product data in spreadsheets, EDI, or on paper, then it is going to be very difficult to trace back during an event.
- Coordination challenges
The more massive and complex your supply chain is, the greater the risk. If you don’t have end-to-end visibility for all of your orders, you put yourself at risk during a recall.
Solving Traceability Problems
iTradeNetwork has just unveiled the industry’s only machine learning-based traceability solution, which allows for instant collaboration between suppliers and buyers so contaminated products can be immediately located and removed from the supply chain.
Through the power of trading data from its 8,000+ member network, iTradeNetwork has enhanced its traceability platform, with no labels or implementation required. Instead, PTI data is captured and associated with the purchase order digitally via machine learning, allowing full path visibility and traceability, removing the need for printing.
How it Works
iTradeNetwork’s incident and recall management solution is the only traceability technology in the industry that allows you to:
- Receive immediate, automatic CDC and FDA recall alerts on the contamination event through our early warning system.
- Instantly identify specific recalled product and remove from the supply chain – pre-shipment, in-transit, and in-store.
- Issue a recall within seconds with specific information to your customers so you can protect them from becoming ill.
iTradeNetwork CEO Rhonda Bassett-Spiers recently shared with Winsight Grocer how this modern traceability solution takes recall response to a whole new level: “Our newer [traceability solution] adds machine-learning capability so if there is a contamination event, we can pretty much trace where that food originated—the seal, the lot, and ensure that that food is pulled off the shelf. That’s why traceability becomes so important. It’s continuity of supply and it’s also minimizing damage to all of the brand and to a whole seasonal crop.”
Proven Results
To test and validate the effectiveness of its new incident and recall management solution, iTradeNetwork analyzed four major food safety events:
- Outbreak of E. coli Infections Linked to Ground Beef (2019)
- 12 million lbs. of chicken strips due to metal (2019)
- Outbreak of E. coli Infections Linked to Romaine Lettuce (2018 & 2019)
- California-based Onions Linked to Salmonella Outbreak (2020)
When looking at these incidents to see how differently these recalls would’ve been handled with our new traceability solution in place, we discovered we our new solutions would’ve allowed for:
- A dramatically reduced timeframe from alert to an impacted product from days to seconds.
- The end to guesswork that creates a slow recall response. Instead of searching through papers, emails, and clipboards, or “scorched earth” recall protocols, the data allows you the ID the right products that are either in transit or delivered and inform customers quickly so impacted goods can be removed from the supply chain immediately.
Next Steps
The data needed for instant, precise traceability incident & recall management is finally here. Food safety regulations will continue to get stricter to protect the public, so now is the time to start putting a better traceability system in place to close the gap on vulnerabilities, not just for compliance-sake but to protect your customers, brand, and profit margins.
Contact iTradeNetwork to learn more about how our new label-free traceability solution can help your business grow.
What is preventing the fast, precise identification of contaminated products in the event of a food safety event? The lack of data. Data that can immediately, and specifically pinpoint the exact product causing the illness. Data that allows for end-to-end supply chain collaboration so the correct contaminated product is removed. This is what can save lives, save your brand, and save goods from being unnecessarily wasted during a contamination event.
Access to this essential data has not existed for the industry, until now.
iTradeNetwork has cracked the code to instant, precise incident and recall management with the industry’s first and only traceability system that relies on data and machine learning, not just labels. This solution allows you to identify and remove contaminated goods within seconds of an alert from the CDC and FDA, instead of days.
Before we go into how this new technology will transform traceability for the industry and your business, let’s look at why such a modernized traceability solution is important to have as food safety events become more and more common.
Current Food Safety & Recall Response
The push to ensure food safety through traceability has been a major priority for the government and food industry as food recalls have increased in the past decade.
From the industry-led Produce Traceability Initiative (PTI) to the Food and Drug Administration’s proposed stricter rule that would go above and beyond the requirements set in the original 2011 FDA Food Safety Modernization Act (FSMA), increased end-to-end traceability through new rules and regulations will continue in order to protect consumers.
The new requirements of FSMA section 204, Enhancing Tracking and Tracing of Food and Recordkeeping, will mandate:
- How traceability records must be maintained
- You must provide records within 24 hours of a request
- Your data and records are organized electronically, not manually.
This means suppliers and buyers need to be able to modernize their systems not only to adhere to these changing regulations but also to be able to coordinate during a recall event.
Traditional Traceability Challenges
Right now, buyers and suppliers have traceability systems in place, but even with PTI, the traditional solutions still leave businesses to the risks of recalls. Why? Because they are working with incomplete, fragmented data and individual approaches to risk. This lack of collaboration, consistency, and real-time, accurate data is keeping companies from moving forward with faster food safety event responses.
Three of the biggest current problems that impact the time and accuracy of food safety events include:
- Incomplete product origination data
Yes, PTI is a universal standard, but it’s not universally adopted across the supply chain due to cost and process burdens.
- Lack of common, trusted, data
If suppliers and/or retailers are still managing product data in spreadsheets, EDI, or on paper, then it is going to be very difficult to trace back during an event.
- Coordination challenges
The more massive and complex your supply chain is, the greater the risk. If you don’t have end-to-end visibility for all of your orders, you put yourself at risk during a recall.
Solving Traceability Problems
iTradeNetwork has just unveiled the industry’s only machine learning-based traceability solution, which allows for instant collaboration between suppliers and buyers so contaminated products can be immediately located and removed from the supply chain.
Through the power of trading data from its 8,000+ member network, iTradeNetwork has enhanced its traceability platform, with no labels or implementation required. Instead, PTI data is captured and associated with the purchase order digitally via machine learning, allowing full path visibility and traceability, removing the need for printing.
How it Works
iTradeNetwork’s incident and recall management solution is the only traceability technology in the industry that allows you to:
- Receive immediate, automatic CDC and FDA recall alerts on the contamination event through our early warning system.
- Instantly identify specific recalled product and remove from the supply chain – pre-shipment, in-transit, and in-store.
- Issue a recall within seconds with specific information to your customers so you can protect them from becoming ill.
iTradeNetwork CEO Rhonda Bassett-Spiers recently shared with Winsight Grocer how this modern traceability solution takes recall response to a whole new level: “Our newer [traceability solution] adds machine-learning capability so if there is a contamination event, we can pretty much trace where that food originated—the seal, the lot, and ensure that that food is pulled off the shelf. That’s why traceability becomes so important. It’s continuity of supply and it’s also minimizing damage to all of the brand and to a whole seasonal crop.”
Proven Results
To test and validate the effectiveness of its new incident and recall management solution, iTradeNetwork analyzed four major food safety events:
- Outbreak of E. coli Infections Linked to Ground Beef (2019)
- 12 million lbs. of chicken strips due to metal (2019)
- Outbreak of E. coli Infections Linked to Romaine Lettuce (2018 & 2019)
- California-based Onions Linked to Salmonella Outbreak (2020)
When looking at these incidents to see how differently these recalls would’ve been handled with our new traceability solution in place, we discovered we our new solutions would’ve allowed for:
- A dramatically reduced timeframe from alert to an impacted product from days to seconds.
- The end to guesswork that creates a slow recall response. Instead of searching through papers, emails, and clipboards, or “scorched earth” recall protocols, the data allows you the ID the right products that are either in transit or delivered and inform customers quickly so impacted goods can be removed from the supply chain immediately.
Next Steps
The data needed for instant, precise traceability incident & recall management is finally here. Food safety regulations will continue to get stricter to protect the public, so now is the time to start putting a better traceability system in place to close the gap on vulnerabilities, not just for compliance-sake but to protect your customers, brand, and profit margins.
Contact iTradeNetwork to learn more about how our new label-free traceability solution can help your business grow.
Speak to an Expert
Take a closer look at the platform built for buyers and their trading partners
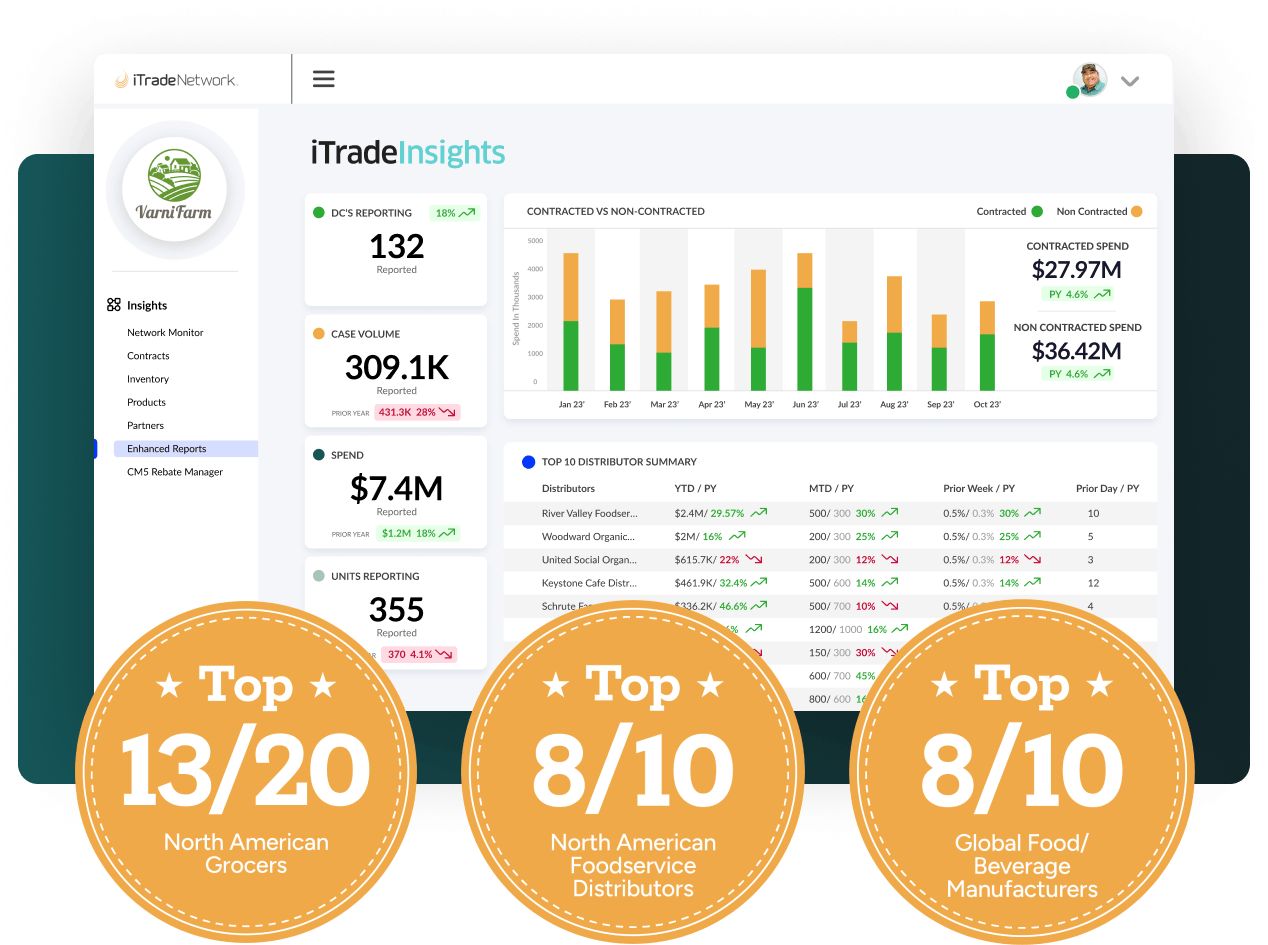
How to Increase Speed and Precision in Recall Management
What is preventing the fast, precise identification of contaminated products in the event of a food safety event? The lack of data. Data that can immediately, and specifically pinpoint the exact product causing the illness. Data that allows for end-to-end supply chain collaboration so the correct contaminated product is removed. This is what can save lives, save your brand, and save goods from being unnecessarily wasted during a contamination event.
Access to this essential data has not existed for the industry, until now.
iTradeNetwork has cracked the code to instant, precise incident and recall management with the industry’s first and only traceability system that relies on data and machine learning, not just labels. This solution allows you to identify and remove contaminated goods within seconds of an alert from the CDC and FDA, instead of days.
Before we go into how this new technology will transform traceability for the industry and your business, let’s look at why such a modernized traceability solution is important to have as food safety events become more and more common.
Current Food Safety & Recall Response
The push to ensure food safety through traceability has been a major priority for the government and food industry as food recalls have increased in the past decade.
From the industry-led Produce Traceability Initiative (PTI) to the Food and Drug Administration’s proposed stricter rule that would go above and beyond the requirements set in the original 2011 FDA Food Safety Modernization Act (FSMA), increased end-to-end traceability through new rules and regulations will continue in order to protect consumers.
The new requirements of FSMA section 204, Enhancing Tracking and Tracing of Food and Recordkeeping, will mandate:
- How traceability records must be maintained
- You must provide records within 24 hours of a request
- Your data and records are organized electronically, not manually.
This means suppliers and buyers need to be able to modernize their systems not only to adhere to these changing regulations but also to be able to coordinate during a recall event.
Traditional Traceability Challenges
Right now, buyers and suppliers have traceability systems in place, but even with PTI, the traditional solutions still leave businesses to the risks of recalls. Why? Because they are working with incomplete, fragmented data and individual approaches to risk. This lack of collaboration, consistency, and real-time, accurate data is keeping companies from moving forward with faster food safety event responses.
Three of the biggest current problems that impact the time and accuracy of food safety events include:
- Incomplete product origination data
Yes, PTI is a universal standard, but it’s not universally adopted across the supply chain due to cost and process burdens.
- Lack of common, trusted, data
If suppliers and/or retailers are still managing product data in spreadsheets, EDI, or on paper, then it is going to be very difficult to trace back during an event.
- Coordination challenges
The more massive and complex your supply chain is, the greater the risk. If you don’t have end-to-end visibility for all of your orders, you put yourself at risk during a recall.
Solving Traceability Problems
iTradeNetwork has just unveiled the industry’s only machine learning-based traceability solution, which allows for instant collaboration between suppliers and buyers so contaminated products can be immediately located and removed from the supply chain.
Through the power of trading data from its 8,000+ member network, iTradeNetwork has enhanced its traceability platform, with no labels or implementation required. Instead, PTI data is captured and associated with the purchase order digitally via machine learning, allowing full path visibility and traceability, removing the need for printing.
How it Works
iTradeNetwork’s incident and recall management solution is the only traceability technology in the industry that allows you to:
- Receive immediate, automatic CDC and FDA recall alerts on the contamination event through our early warning system.
- Instantly identify specific recalled product and remove from the supply chain – pre-shipment, in-transit, and in-store.
- Issue a recall within seconds with specific information to your customers so you can protect them from becoming ill.
iTradeNetwork CEO Rhonda Bassett-Spiers recently shared with Winsight Grocer how this modern traceability solution takes recall response to a whole new level: “Our newer [traceability solution] adds machine-learning capability so if there is a contamination event, we can pretty much trace where that food originated—the seal, the lot, and ensure that that food is pulled off the shelf. That’s why traceability becomes so important. It’s continuity of supply and it’s also minimizing damage to all of the brand and to a whole seasonal crop.”
Proven Results
To test and validate the effectiveness of its new incident and recall management solution, iTradeNetwork analyzed four major food safety events:
- Outbreak of E. coli Infections Linked to Ground Beef (2019)
- 12 million lbs. of chicken strips due to metal (2019)
- Outbreak of E. coli Infections Linked to Romaine Lettuce (2018 & 2019)
- California-based Onions Linked to Salmonella Outbreak (2020)
When looking at these incidents to see how differently these recalls would’ve been handled with our new traceability solution in place, we discovered we our new solutions would’ve allowed for:
- A dramatically reduced timeframe from alert to an impacted product from days to seconds.
- The end to guesswork that creates a slow recall response. Instead of searching through papers, emails, and clipboards, or “scorched earth” recall protocols, the data allows you the ID the right products that are either in transit or delivered and inform customers quickly so impacted goods can be removed from the supply chain immediately.
Next Steps
The data needed for instant, precise traceability incident & recall management is finally here. Food safety regulations will continue to get stricter to protect the public, so now is the time to start putting a better traceability system in place to close the gap on vulnerabilities, not just for compliance-sake but to protect your customers, brand, and profit margins.
Contact iTradeNetwork to learn more about how our new label-free traceability solution can help your business grow.